
Concrete Surface Scaling
One of the most common failure investigations we do routinely perform is related to scaling or loss of the original finished surface of concrete slab. Being in the east coast, such projects often increase in numbers right after the winter seasons when the effects of harsh winter weather conditions and applications of deicing salts take the toll on concrete roads, bridge decks, sidewalks, driveways, parking garages, and other structures that have been exposed to snow, ice, and salts. The most common question to address is whether the surface scaling is due to poor quality of the concrete, or improper construction practices, or potentially deleterious roles of deicing salts, or a combination of these.
Scaling, Mortar Lift-off, and Aggregate Popout
Three common types of surface distress
During investigation of surface scaling of an outdoor concrete slab, the slab surface usually shows one or a combination of following three different types of distresses that are often closely related:
-
Scaling - Loss of the original finished surface of slab causing exposures of underlying mortar fraction and coarse aggregate particles of concrete, which can occur in some small isolated patchy areas to larger scale. The depth and severity of scaling may be limited to light to moderate scaling with exposures of only the mortar fraction to severe scaling when near-surface coarse aggregate particles are exposed.
-
Mortar Lift-off - In mortar lift-off, the exposed coarse aggregate particles are present in sound conditions without any fracturing or distress, only the top thin sheet of surface mortar cover over the near-surface (now exposed) coarse aggregate particle is lost. Usually the weak bond between the finished surface mortar and underlying near-surface coarse aggregate particles causes the surface mortar to lift off from the coarse aggregate particles. The weak bond could develop from a number of reasons, e.g., inadequate curing of the finished surface, inadequate embedding of the coarse aggregate particles, prolonged finishing of surface over flat topsides of near-surface coarse aggregate particles, finishing operations with excess water at the surface either from water added during finishing and/or from finishing with bleed water on the surface, deleterious actions of salts on the surface mortar, etc. Mortar lift-off can occur from weak bonds between the finished surface and underlying near-surface flat topsides of aggregate particles where repeated finishing passes and/or the presence of a soft paste susceptible to disintegrate can cause apparent loss of the finished surface exposing the nearby aggregate.
-
Aggregate Popout - By contrast, in aggregate popouts, the exposed aggregate itself is unsound, which has expanded in the presence of moisture and freezing, thus popped out and fractured from absorption of moisture and subsequent freezing leaving fractured remains of the unsound particle at the surface often with a conical depression from fracturing and loss of aggregate. Other mechanisms such as deleterious alkali-aggregate reactions of unsound aggregate at the surface region, especially if the surface is saturated with moisture and high alkalis can also contribute to aggregate popout. Both physical and chemical deterioration processes of unsound near-surface aggregate particles can cause popout to not only fracture the aggregate but lift-off the surface mortar above it, often creating a conical depressions in the fractured aggregates. Inadequate embedding of such unsound aggregates by a dense, impermeable surface mortar increases the frequency of occurrences of such popouts.
​
Therefore, surface scaling, mortar lift-off, and aggregate popout can occur from cyclic freezing and thawing of concrete, or, from improper finishing. Both can aggravate the surface condition once deicing salts appear into the scene.
Due to the common hygroscopic natures of most road salts, applications of deicing salts increases the degree of saturation of concrete at the surface, which, in turn, increases the vulnerability to scaling, especially if the surface is not of dense, impermeable nature and has a good air void system. Deicing salts can deteriorate surface regions of slabs by various ways, e.g.,
-
From physical actions, e.g., by formation of expansive calcium oxychloride by reactions between calcium chloride salt and calcium hydroxide component of cement hydration in paste, or calcium chloro-aluminate based (Friedel's) salt by similar reactions with calcium aluminate hydrate component of cement hydration at the surface
-
Chemical decomposition of paste by replacing the calcium-silicate-hydrate component of paste from an attack from magnesium chloride or sulfate based salt, actions of salts on concrete can be both physical and/or chemical in nature, which can occur even in a good quality concrete, placed and finished following proper industry guidelines.
-
Even an early exposure of common sodium or calcium chloride based salts (during late Fall, winter, or early Spring constructions) prior to the attainment of concrete maturity (a period of air drying and a compressive strength of at least 4000 psi) can cause salt scaling.
Even without any deicing salts, simple loss of the original finished surface can occur from:
-
Freezing of a non-air-entrained or a poorly air-entrained concrete at critically saturated conditions (i.e., a condition when more than 91% of capillary pore spaces in paste are filled with freezable water), especially at the surface region, which was in direct contact with freezing weather during service, or
-
Freezing of a soft, porous finished surface at the freezing front due to finishing in the presence of excess water at the surface.
​
To be resistant to freezing and salt exposure-related surface scaling, an outdoor concrete should be (Jana 2004, 2005):
-
Adequately air-entrained, i.e., having an air content of around 4½ to 6½ percent with an air void specific surface of at least 600 in2/in3 and an air void-spacing factor of maximum 0.008 in;
-
Concrete should be made using a low water-cementitious materials ratio (w/cm) mix of a maximum 0.45 ratio,
-
Should have a 28-day compressive strength of at least 4000 psi, and preferably 4500 psi if exposed to moisture, salts, and snow,
-
Concrete should have achieved the necessary maturity of at least 4000-4500 psi strength and a period of air drying to remove all evaporable water prior to the first exposure of salt and snow,
-
Concrete should be placed, consolidated, and finished properly to remove any coarse voids from inadequate consolidation, and excess water, or water accumulation at the surface region during finishing, and
-
Should be adequately cured to assure adequate hydration of cement at the optimum temperature and relative humidity conditions at the surface.
​
Fulfillment of all these essential conditions provide an assurance of a good resistance to common sodium or calcium chloride-based deicing salts, unless:
-
Salt is applied at an early stage, e.g., prior to the attainment of maturity when concrete does not develop sufficient strength to prevent physical actions of salts, or,
-
A physically or chemically aggressive (e.g., magnesium sulfate, urea-based) salt is used, or if expansive crystals (e.g., calcium oxychloride, calcium chloro-aluminate) form from deleterious reactions between a calcium chloride deicer and calcium hydroxide or calcium aluminate hydrate components of Portland cement hydration.
Therefore, any reported surface scaling distress questions fulfillment of the above-mentioned conditions i.e., from concrete quality to the construction practices since inadequacy in concrete quality and/or improper finishing/curing practices would reduce the freeze-thaw durability and resistance of surface to salt and would cause (or aggravate) surface distress. In such cases, it is not just the salt itself to blame, since any outdoor concrete is expected to have some salt exposures in severe weather conditions, but the overall quality of concrete and how it was constructed determine the ultimate resistance of slab to the potentially deleterious actions of salts.
Scaling
-
Loss of original finished surface of mortar
-
Common causes - Lack of entrained air, low air, loss of air at surface region, improper air void system, finishing improprieties (premature finishing prior to cessation of bleeding, prolonged finishing, finishing with excess water at surface, inadequate curing, exposures to deletrious salts
-
Tests done - Petrographic examinations (ASTM C 856), detailed air void analysis (ASTM C 457), water or acid-soluble chloride contents at the surface region and interior of concrete slab (ASTM C 1152, C 1218), compressive strength of concrete (ASTM C 42).

Mortar Lift-off
-
Loss of finished surface over flat, topsides of near-surface aggregate particles
-
Common causes are - Inadequate embedding of aggregates by surface mortar, premature finishing, prolonged finishing of surface over flat topsides of near-surface aggregates, inadequate curing
-
Exposed aggregates are usually present in sound condition with contributing to the distress

Aggregate Popout
-
Fractured remains of unsound near-surface aggregate particles, usually leaving a conical depression at the fractured remains
-
Common causes are - Volume expansion of unsound aggregate by moisture absorption, freezing at critically saturated condition, alkali-aggregate reactions, etc.
-
Needed to determine the amount of popout-forming particles in aggregate and either they are accidental contaminants and present only at the surface region, or inherent component of the aggregate used and seen all through out the slab (core).
Send us an email at info@cmc-concrete.com with any questions, or call us at 724-834-3551
The Scaling Triangle & Top 10 Factors
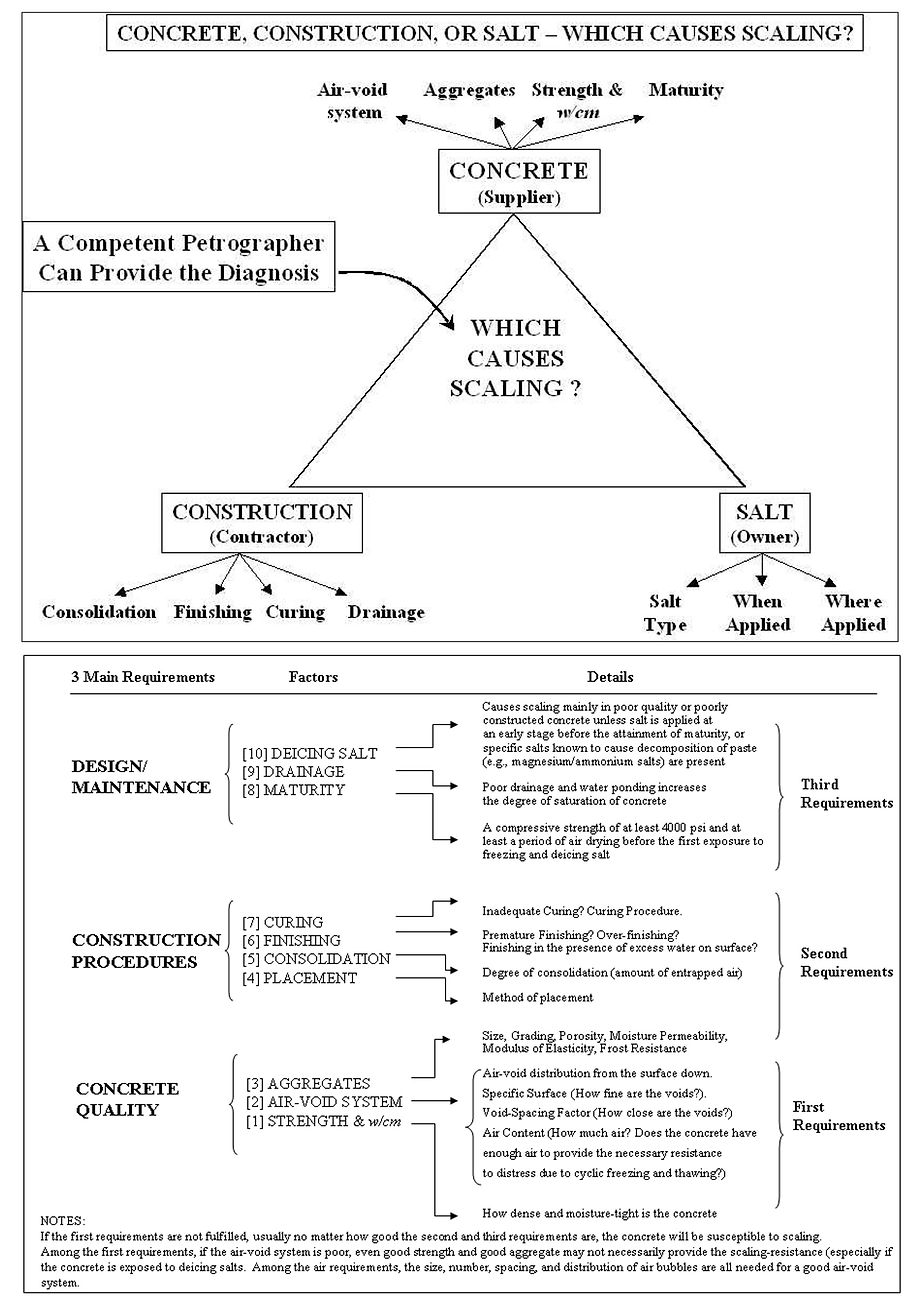
Surface scaling of a non-air-entrained concrete exposed to deicing salts
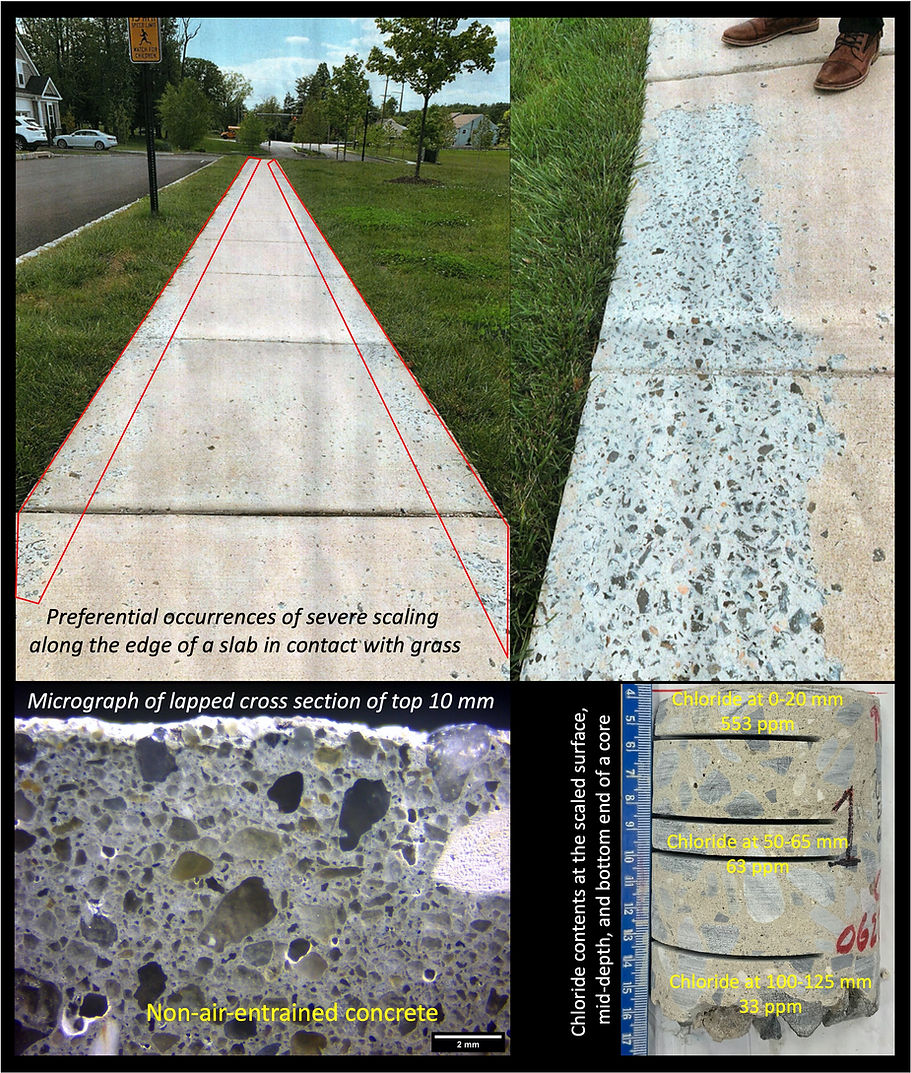
Surface scaling from finishing improprieties

Surface scaling from inadequate curing, lack of entrained air at the surface, and exposures to deicing salts

Surface Scaling & Aggregate popout

Surface scaling from finishing improprieties and exposures to deicing salts

Aggregate popout from unsound shale or limestone in coarse aggregate

Aggregate popout from porous chert gravels
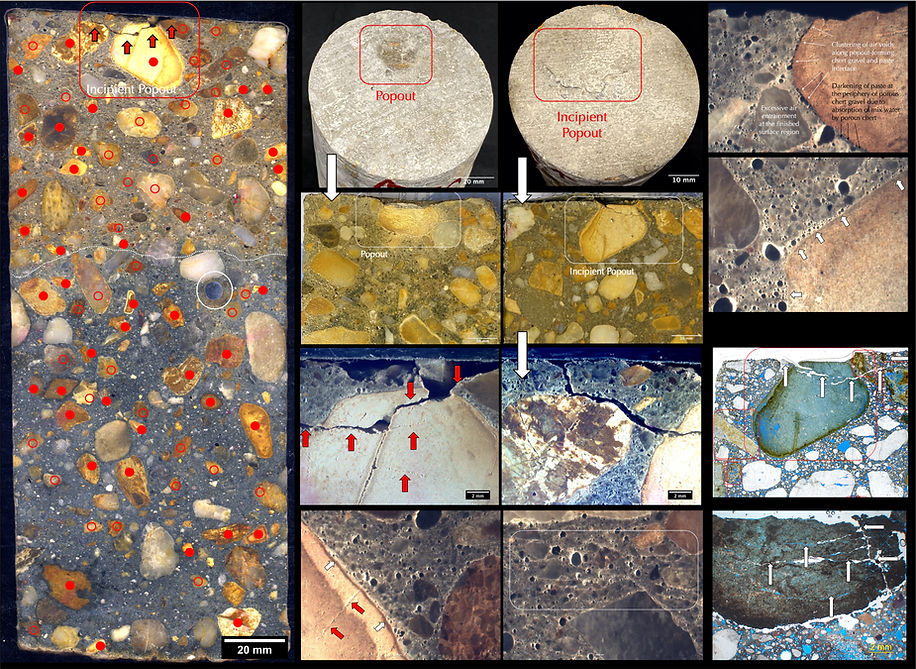
Various surface distress and scaling projects of CMC

Concrete scaling from poor air-void system
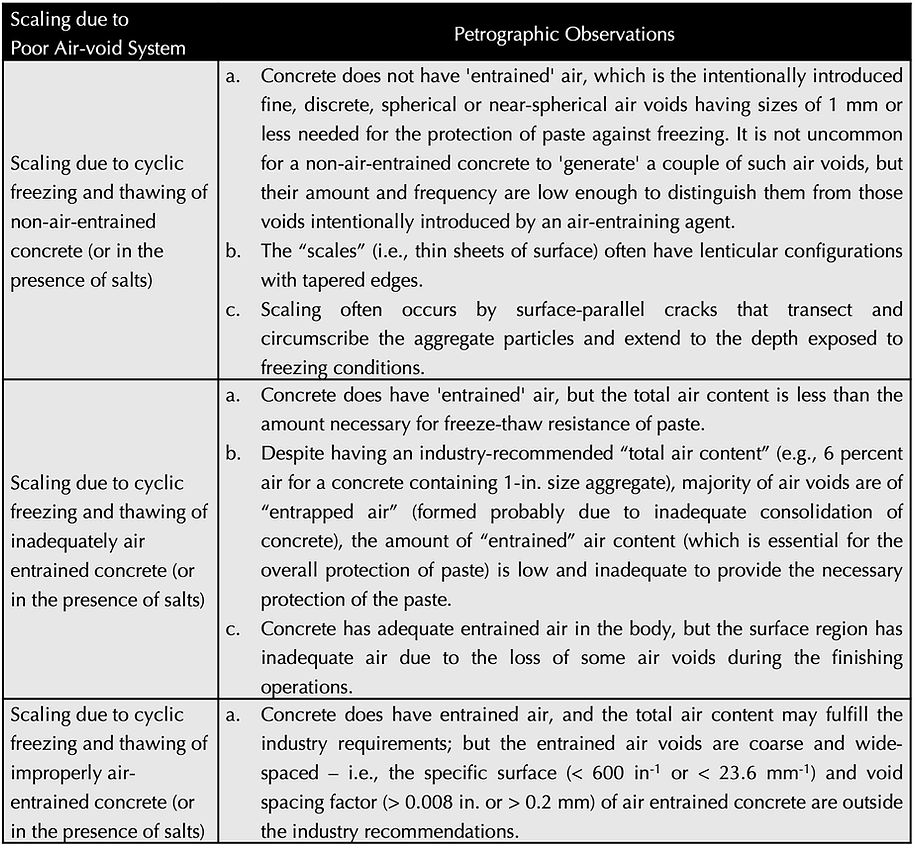
Concrete scaling from finishing improprieties

Concrete scaling from deicing salts

Our Work in ACI Publications
Click on the images or texts to download the entire publication
Click on the images or texts to download the entire publication
Scaling of concrete pavements, sidewalks, driveways, decks, and other slabs is a common problem in outdoor construction exposed to severe winter weather and deicing salts. Very often, the blame circulates around the quality of the concrete supplied (to the supplier), the methods of construction used (to the contractor), or the salt applied for snow removal (to the owner). Among these three, the most common culprit is assumed to be the deicing salt. The dispute is usually settled by field investigation, detailed petrographic examinations, air-void analysis, chloride analysis of concrete cores or saw-cut sections from the scaled and sound areas of a slab, and investigation of the various factors responsible for scaling.
​
Part I of this article provides three case studies that demonstrate the roles of lack of air entrainment, improper air entrainment (coarse air void system), and inadequate air entrainment (low entrained air content) in scaling. Part II will provide three case studies to show scaling due to the initiation of finishing prior to the cessation of bleeding, finishing in the presence of excess water at the surface, and prolonged finishing practices. A poor air-void system causes scaling of the concrete surface at saturated conditions during cyclic freezing and thawing. Finishing improprieties, on the other hand, can cause scaling, abrasion, or delamination even in the absence of cyclic freezing and thawing
Scaling of concrete surfaces is a common problem in many outdoor slabs exposed to deicing salts and cyclic freezing and thawing. Despite occurrences of adjacent panels—one perfectly sound while the other severely scaled—exposed to the same deicing conditions, salt is, allegedly, the most common culprit of scaling. The first part of this two-part article described how a poor air-void system can cause surface scaling in concrete. In all case studies described, concrete scaling was initiated due to the poor air-void system and was aggravated by the presence of deicing salts. Concrete with a good air-void system showed much better resistance to freezing and salt than that with a poor air-void system.
​
This second part describes three additional case studies where, despite having good air-void systems, the concrete scaled due to improper finishing practices such as: a) initiation of finishing prior to the cessation of bleeding (entrapping bleed water under the finished surface); b) finishing in the presence of excess water at the surface, which reduces the scaling and abrasion resistance of the surface; and c) prolonged finishing, which severely reduces the air content at the surface and increases the concrete’s potential to scale.
​
Our Work in ICMA Proceedings
Scaling, i.e., local flaking or peeling away of the near-surface portion of a concrete slab is the most common type of surface distress, especially in areas exposed to cyclic freezing and thawing, and deicing chemicals. A comprehensive evaluation of factors responsible for concrete surface scaling is presented. The article gives a close look to the influences of: (a) concrete materials, proportions, and properties (air content, air void system, aggregate, cement paste, aggregate-paste interface, compressive strength, water-cementitious materials ratio, degree of saturation of concrete, and chemical admixtures); (b) construction practices (consolidation, finishing, curing, hot and cold weather protections, drainage, and surface treatments); (c) concrete maturity; and (d) deicing salts (salt type, concentration, timing of exposure) on scaling. The evaluation is based on numerous case studies on field reconnaissance and laboratory investigation of concrete scaling, where holistic approaches incorporating all possible factors for scaling were considered.
​
Our Work in Concrete Construction Magazine
When scaling due to cyclic freezing occurs, often the cause is judged to be de-icing chemicals, particularly calcium chloride. It’s the easy one to blame because it is so commonly used, and it has, through the years, become the scapegoat of scaling distress.
In our experience, though, concrete that has attained maturity (or near maturity), that has an air-void system that meets industry standards, and that is properly made, cured, and finished, will be resistant to the damaging effects of cyclic freezing and de-icing chemicals. The need for concrete “maturity” is emphasized in the ACI Committee 201.2R report (Guide to Durable Concrete) that states, “Before being exposed to extended freezing while critically saturated ... concrete should attain a compressive strength of about 4000 psi. A period of air drying following curing is advisable.” We recommend that the concrete achieve a compressive strength of about 3000 psi for moderate exposure.
Our experience, based upon detailed laboratory studies of thousands of samples, attests to the durability of concrete sidewalks and driveways that are:
â– made with good-quality air-entrained concrete
â– constructed using sound construction practices
â– allowed to “mature” before exposure to cyclic freezing and de-icing chemicals.
Fee Schedule

Report Turnaround Time
​Standard: 3-4 weeks
Expedite: 3-5 business days